Right about the time we glued up the legs for headboard-end of our platform beds and were starting to contemplate the next step which involved mortise and tenon joinery, Maverick decided we need to practice a little before we potentially ruined our beautiful (and expensive) maple. He found some plans for a shaker "saturday" table in one of his woodworking magazines. I have no idea why it's called a "Saturday" table.
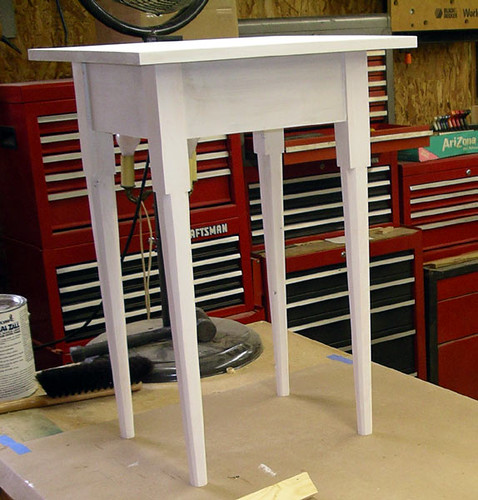
Other than some crazy looking tapered octagonal legs it seemed like a pretty straight forward small piece of furniture that would require the apron to be attached to the legs with simple mortise and tenon joints. Maverick's plan was to use basic scrap lumber he had lying around the shop and he went ahead and built one pretty quickly.
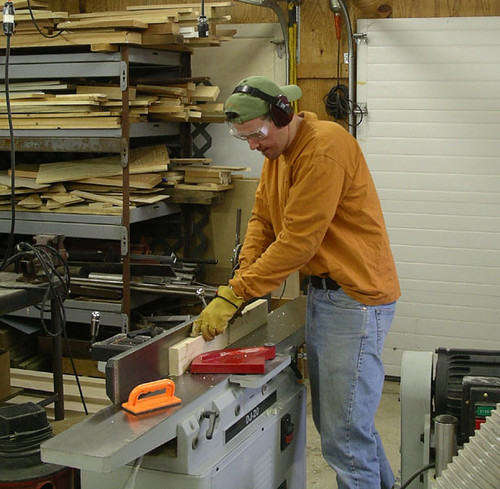
Let me take this opportunity to make a basic observation about Maverick: he has never met a woodworking jig, tool, or gadget that he hasn't fallen in love with. So Maverick happens to own a mortise cutter (something I never would have even guessed existed a few weeks ago.) I am certainly not complaining about Maverick's acquisitive habits and in fact I am benefiting greatly from his impressive tool collection. (He also appears to be in some sort of tool arms-race with our friend KD).
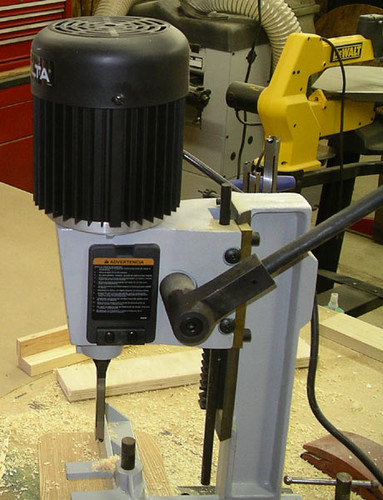
So Maverick went ahead and whipped one of these tables out last week and I have to say it turned out very nicely. Since he had used crappy pine 2x4s and some old poplar, he painted it, but I would guess that if he had made it with walnut as the plans called for it would have looked very presentable.
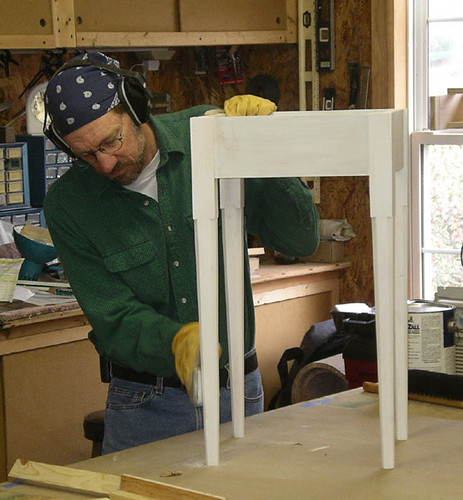
On Saturday it was my turn to make the table. While Maverick primed, sanded, and primed his table I was hard at work at the jointer, planer and table saw getting my scrap lumber ready to be transformed into a "saturday" table, too.
The tricky part of the table is the legs and these are made possible by a jig that, luckily, Maverick had already created for his table.
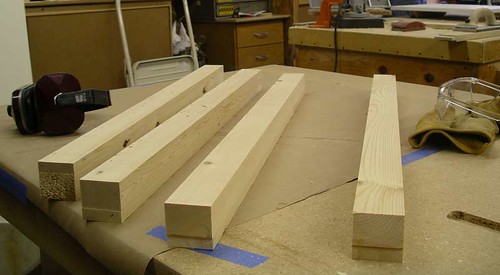
After getting little help with how the jig worked I was quickly screwing up my first leg. My mistake was two-fold: first I had never used a band saw before so it took me a little bit to get a feel for it, second when it came time to use the jointer to clean up the rough-cut tapers on the leg I jointed a little bit too high and took some wood off the part of the leg that has to be straight in order to connect to the apron.
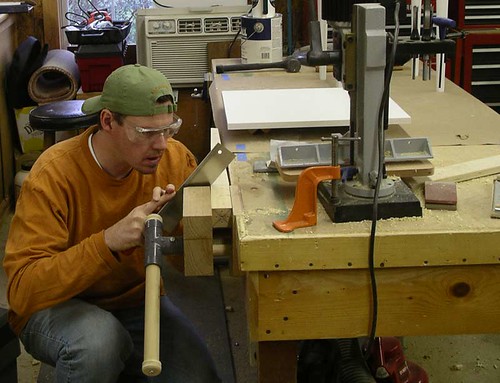
The second leg was much better, but still had the jointer problem. I ran out of time before I could screw up the next 2 legs. I talked to Maverick today at work and he thinks I should just make 2 more legs and write-off the first two. I may do this.